What is Meant by Predictive Maintenance
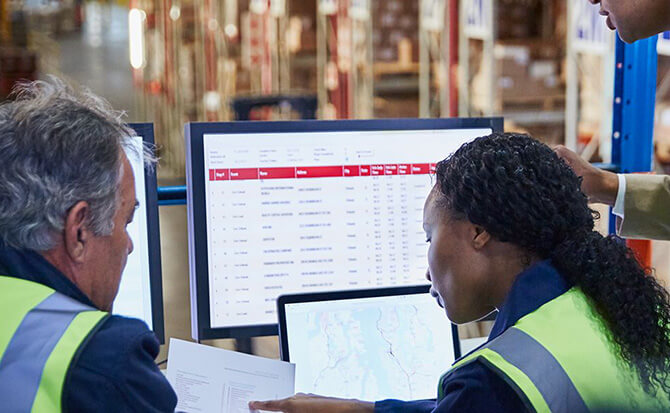
Predictive maintenance is a novel approach to asset management that transforms traditional maintenance paradigms by leveraging modern technologies to anticipate and prevent failures. By continuously analyzing real-time data and utilizing artificial intelligence programs, predictive maintenance enables companies to act proactively, avoiding costly downtime and extending the lifespan of equipment. Rather than waiting for malfunctions to occur, this method allows for preventive intervention, benefiting productivity and reducing maintenance-related costs.
What is Predictive Maintenance?
Predictive maintenance encompasses a set of sophisticated techniques and tools used to continuously monitor the operational conditions of assets with the goal of predicting and preventing failures or malfunctions before they occur. It marks a significant improvement over traditional preventive maintenance, which relies on scheduled interventions at fixed intervals, often suboptimal. In contrast, predictive maintenance utilizes real-time data to accurately determine the actual condition of machinery, allowing maintenance activities to be scheduled only when truly necessary.
How does it work? The approach relies on a combination of advanced sensors, data analysis, and machine learning algorithms. Sensors are installed on assets to collect various operational data, such as vibrations, temperature, pressure, and energy consumption. This information is then transmitted to centralized analysis systems, where machine learning algorithms process the data to detect signs of degradation and system anomalies.
However, predictive maintenance is not limited to detecting imminent problems; it also enables long-term optimization of asset management. Through continuous data analysis, companies can identify the root causes of recurring failures, improve production processes, and more effectively plan asset replacements or repairs. This proactive approach enhances asset reliability and availability while simultaneously reducing overall operational costs.
Technologies Behind Predictive Maintenance
Predictive maintenance leverages several key technologies that work synergistically to monitor, analyze, and predict the operational conditions of business assets. The Internet of Things (IoT) plays a fundamental role in this process, enabling continuous data collection from sensors installed on assets. A wide range of parameters is monitored, including vibrations, temperature, pressure, humidity, and energy consumption, providing a constant flow of detailed information on the state of machinery.
Once collected, the data is transmitted to cloud-based analysis platforms, where artificial intelligence (AI) and machine learning (ML) algorithms come into play. Designed to process large volumes of data in real-time, these algorithms identify complex patterns and anomalies that may indicate imminent degradation or potential failure. By utilizing machine learning techniques, these systems can continuously improve their predictive capabilities, learning from historical data and adapting to new information.
In addition to sensors and algorithms, another crucial technology is digital twins. These are virtual models of physical assets that replicate their behavior and operating conditions. Digital twins allow for the simulation of various scenarios and operating conditions, testing maintenance strategies, and predicting the impact of decisions without interfering with real-world operations.
Predictive maintenance technologies are tightly integrated into Enterprise Asset Management (EAM) systems. EAM systems provide a centralized platform for asset management, enabling a coordinated view of maintenance operations. Integrating predictive maintenance technologies into EAM systems enhances planning, optimizes resource allocation, and supports decisions based on accurate and up-to-date data.
Benefits of Predictive Maintenance
Adopting predictive maintenance offers numerous advantages for companies. Firstly, it reduces unplanned downtime, thereby increasing productivity and operational efficiency. By continuously monitoring asset conditions and intervening only when necessary, unexpected interruptions that can lead to production losses and high costs are avoided.
Another key benefit is the reduction of costs associated with preventive and corrective maintenance. Since maintenance activities are scheduled based on real data and accurate predictions, unnecessary expenses linked to superfluous interventions are eliminated. This targeted approach allows for better resource allocation.
Thirdly, constant asset monitoring enables the extension of their useful life. Early signs of wear and degradation are detected immediately, allowing timely interventions that prevent more severe damage and prolong asset lifespan.
A significant benefit is the enhancement of operational safety. By identifying and addressing potential issues before they cause accidents or significant damage, a proactive approach reduces the risk of workplace injuries and costly equipment damage. A safer operational environment translates into lower insurance and legal costs for the company.
Lastly, there is an undeniable competitive advantage. Organizations that adopt predictive maintenance can operate more efficiently and responsively, improving service quality and customer satisfaction. Optimizing operations and reducing downtime enable quicker responses to market demands, strengthening the company’s position in the industry.
Predictive maintenance is particularly crucial in sectors like aerospace, where safety and reliability are paramount. Advanced sensors and AI algorithms detect anomalies before they become serious problems, ensuring optimal performance and safety standards.
Best Practices for Effective Predictive Maintenance
To maximize the benefits of predictive maintenance, it is important to follow some best practices that ensure its effectiveness and efficiency. These practices not only optimize the predictive maintenance process but also contribute to improving asset reliability.
First and foremost, begin with a thorough analysis of business needs and critical assets to identify areas where predictive maintenance can provide the greatest benefits. Focus resources and investments on assets that most influence productivity and profitability.
Selecting the appropriate sensors and technologies is crucial to ensure the quality and reliability of the data collected. Choose sensors based on the specific parameters of the assets to be monitored, and ensure they are robust enough to operate in harsh industrial environments.
It is also essential to train personnel on new technologies and methodologies. Promoting a culture oriented toward predictive maintenance involves encouraging continuous improvement and innovation, creating an environment where staff feel supported and motivated to contribute to the program’s success.
Another key aspect is continuous monitoring of results. Predictive maintenance is a dynamic process that requires constant verification of asset performance and monitoring systems. By doing so, maintenance strategies can be adjusted based on feedback obtained, improving operations and responding promptly to any anomalies.
IFS Solutions Offered by FI Solutions
To support business growth and implement effective predictive maintenance solutions, FI Solutions offers a comprehensive range of innovative digital solutions developed by IFS. Among these are advanced EAM systems.
Within IFS Cloud, both ERP and FSM applications also ensure high performance and meet every specific need.
These solutions enable data-driven processes and allow companies to maximize the potential of digital transformation. With IFS’s technological expertise and FI Solutions’ specialized consultancy, client companies are guided in addressing market challenges and fully exploiting opportunities for change.