4 Key Predictions for the Manufacturing Industry in 2024
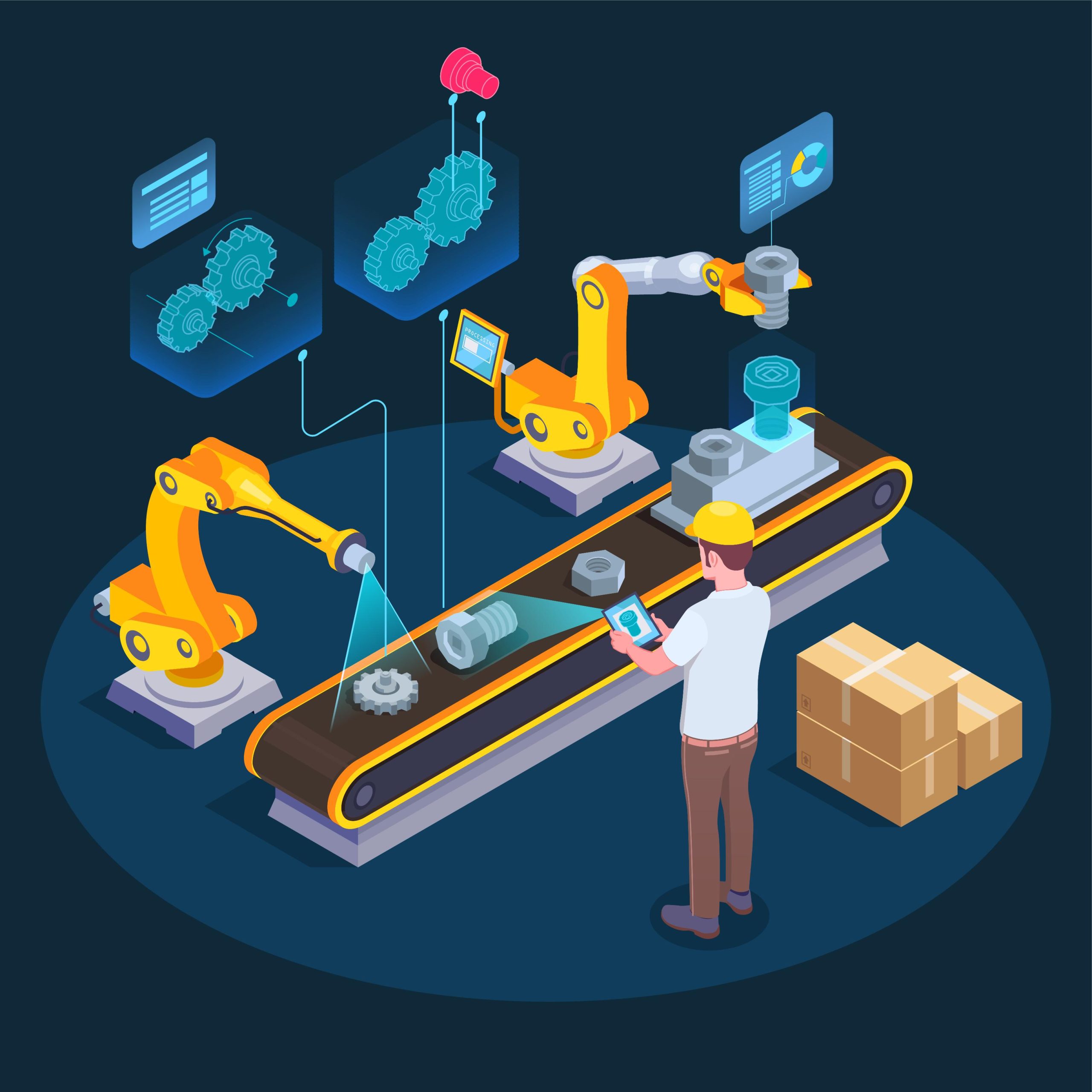
Written by Maggie Slowik, Global Industry Director Manufacturing at IFS
Manufacturers faced intense challenges in 2023, including increased competition, complex customer demands, and stricter regulations. To maintain a competitive edge in 2024, adopting new technologies to alleviate volatility is crucial. This technological adoption will help manufacturers manage increased volatility effectively and differentiate themselves in the market.
Maggie Slowik and Andrew Burton delve into market insights in their 2024 predictions, pinpointing four key forecasts that are set to bolster business resilience in the manufacturing industry.
Prediction #1: Artificial Intelligence and Data Pattern Recognition
In the next three years, there is an expected 40% increase in investment and demand for AI and data pattern recognition.
Over the same period, AI spending in the IT sector is projected to rise by 40%. This heightened investment is poised to enhance manufacturing efficiency through the implementation of AI data pattern recognition. Utilizing historical data, AI can rapidly analyze real-time production data, detecting patterns and anomalies. The enduring value of AI and data pattern recognition lies in providing manufacturers with continuous root cause analysis, workflow optimization, and the ability to predict potential product quality issues by comparing various data points.
As manufacturing systems become more intricate, the role of AI-driven data pattern recognition becomes critical for refining quality control, predicting equipment issues, and optimizing production to achieve fewer defects, higher Overall Equipment Effectiveness (OEE), and substantial cost savings.
In the era of Industry 4.0 and the emerging Industry 5.0, where an overwhelming amount of data is generated every second, AI is poised to become an indispensable tool for manufacturers, surpassing the cognitive capacity of the human mind to handle such data influx.
Prediction #2: Dynamic Planning and Digital Maturity
In the next 2-5 years, manufacturers with advanced digital maturity will embrace dynamic planning by incorporating AI-powered technology to enhance their Enterprise Asset Management (EAM) and Enterprise Resource Planning (ERP) systems.
The conventional static planning approach is no longer adequate for contemporary manufacturing. According to McKinsey, the utilization of AI pattern recognition tools can result in a 4% increase in revenue, a potential reduction in inventory by up to 20%, and a decrease in supply chain costs by as much as 10%.
Recent research from IFS indicates that manufacturers are persistently grappling with ongoing challenges in their supply chains. Nevertheless, by harnessing the capabilities of AI, ERP, and EAM, manufacturers can optimize their inventory, allocate resources efficiently, and utilize real-time machine data. Integration of AI-powered tools equips manufacturers to promptly respond to shifts in demand, disruptions in the supply chain, and fluctuations in the market.
For instance, the incorporation of AI within ERP systems enables manufacturers to quickly adapt to unforeseen changes in raw materials, predicting potential delays from suppliers. This proactive approach enhances adaptability, reduces lead time, and minimizes the impact of supply chain disruptions, thereby promoting efficient production.
Prediction #3: The Talent Crisis and Technology’s Role for Workers
The global manufacturing industry is in the grip of a deep talent crisis, with 78% of firms in construction, production, manufacturing, and logistics struggling to recruit skilled workers, according to the British Chambers of Commerce (BCC). Aging workforces and changing work ethics, intensified by the COVID-19 pandemic, contribute to the crisis, causing disruptions in productivity due to increased employee turnover.
A recent IFS Customer Advisory Board meeting emphasized that acquiring skills is only part of the challenge; training and retaining talent are equally crucial. Manufacturers recognize the need for technology integration to improve productivity, with 62% acknowledging the potential of better tech tools, and 58% stating increased technology needs in the last five years.
An IDC study commissioned by IFS highlighted that 45% of manufacturers prioritize enhancing the worker experience through technology. The concept of the ‘connected worker,’ involving employees in technology integration, can drive productivity, efficiency, and improve the shop-floor worker experience, potentially unlocking over $100 billion in value for the industry.
Connected worker technology and digital collaboration have the potential to boost productivity by 20-30% in intensive work processes. Acknowledging people as a company’s most critical asset, connected worker tools and platforms can enhance engagement, productivity, and job satisfaction, providing a competitive edge. Looking ahead, AI is expected to play a crucial role in further empowering the connected worker by offering insights and accuracy to improve efficiency.
Prediction #4: Circularity Strategies in Business Models
By 2025, 30% of manufacturers are expected to integrate circularity strategies into their business models, initially aimed at reducing waste and enhancing resource efficiency. Linear business models, characterized by a “take-make-waste” approach, are increasingly deemed unsustainable, unpopular, and prone to business risks.
Approximately 42% of global manufacturers express concerns about the scarcity of key supplies and rising raw material costs. To mitigate dependence on raw materials and bolster resilience, manufacturers must reevaluate their business models and embrace circularity. Bain & Company reports that 33% of executives anticipate disruption from circularity start-ups, which reintegrate products or materials into the supply chain, enhancing resilience and profitability.
The urgency for circularity is amplified as regulatory landscapes evolve rapidly in the UK, Europe, and the US. Policies like the European Green Deal are accelerating the transition to a circular economy. Manufacturers preparing for this shift require appropriate technology. Designing for circularity is crucial, as around 80% of product-related environmental impacts are determined during the product design phase. Manufacturers need to consider material choices, supplier decisions, and redesigning products to facilitate disassembly, repair, and recycling for future circularity.
The industry needs efficient handling of returns and incorporation of reverse logistics, recognized by Gartner as a key driver for circularity strategies. This circular business model allows manufacturers to efficiently return end-of-life goods, minimizing waste. Traceability is another essential capability for circularity, enabling manufacturers to track materials, parts, and products throughout their lifecycle. This ensures continuous awareness of a product’s journey and environmental impact.
Fostering innovation, resilience, and circularity in the journey towards 2024
Manufacturers are accustomed to confronting numerous challenges. Their unwavering resilience propels innovation, as they embrace crucial technologies to improve operations. Moving into 2024 and beyond, their focus on efficiency and optimization will be critical for maintaining a competitive edge.