The AI revolution in manufacturing: from science fiction to smart factories
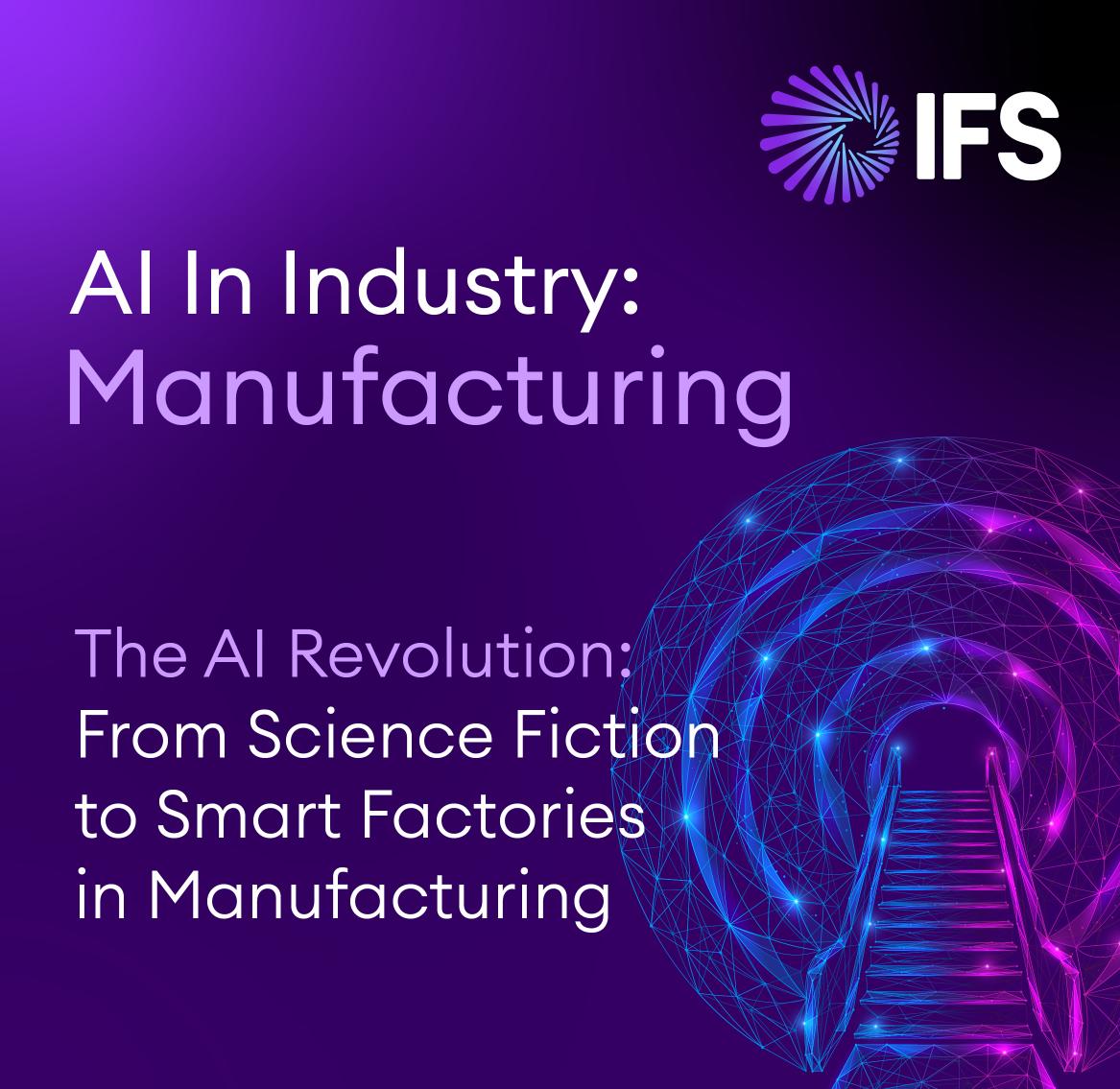
The manufacturing industry has gone through a rapid period of transformation, leveraging digital technology to improve its operations and gaining significant operational and efficiency gains in return.
However, with the advent of more advanced technologies and models such as Industry 4.0, data transformation and smart factories, Artificial Intelligence now stands as the technological force that will truly reshape the industry from the ground up.
No longer relegated to science fiction, AI integration is truly taking hold in the industry, ushering in a new era of smart manufacturing. Using powerful algorithms and data analytics, AI is enabling manufacturers to optimize processes, improve product quality and streamline operations.
AI Use Cases in the Manufacturing Sector
In this article we will delve into specific use cases, highlighting how AI is revolutionizing manufacturing and exploring its profound impact on the way we create, assemble, and deliver products to the world. As manufacturing companies move into the AI era, they will have powerful tools at their disposal to improve productivity, reduce costs and ensure the highest quality standards.
Embracing these innovations and recognizing the importance of quality data will be key to thriving in the ever-changing landscape of modern manufacturing.
Business Simulation and Digital Twins
Generative artificial intelligence is leading to the development of sophisticated digital twin models. These digital replicas of physical manufacturing systems enable real-time simulation, monitoring and optimization. By leveraging digital twins, manufacturing companies have the ability to test and refine their processes virtually, reducing downtime and improving overall efficiency. Generative AI continuously updates these models, ensuring that they are always accurate and reflect the changing manufacturing environment.
Forecasting Supply and Demand with AI
With its digital twin, manufacturing companies can gain valuable insights and adapt to changing market demands. By leveraging artificial intelligence in the areas of supply and demand forecasting (supply and demand forecasting), scheduling and planning optimization, manufacturing companies can optimize their operations for maximum efficiency.
In addition, with continuing challenges related to rising labor, raw material and supply chain costs, AI has the potential to help the industry overcome economic difficulties and gain a competitive advantage. Demand forecasting is a crucial component of modern manufacturing. When combined with external data feeds and AI-powered insights, it will undergo a significant transformation. Integrating AI with demand forecasting offers a wide range of possibilities, improving the accuracy of forecasting.
For example, customers whose sales depend on weather conditions, such as the food and beverage industry, can expect an increase in forecast accuracy of up to 78 percent over existing demand planning models. Event-driven demand prediction, powered by external factors such as weather conditions, uses the power of AI to anticipate changes in demand that might otherwise be overlooked. By taking these factors into account, manufacturers can prepare for market changes more effectively.
Supply Chain Optimization with AI
Supply chain management constitutes a complex ecosystem that is set to undergo significant transformation through the intervention of AI.
Equipped with advanced algorithms and data analysis capabilities, AI helps optimize this intricate network by predicting demand patterns, managing inventories and designing efficient logistics routes. By taking a proactive approach, AI ensures that manufacturers remain agile and minimize delays or overstocking situations. In this way, the supply chain process becomes more efficient and effective overall.
Optimizing Planning with AI
Industrial manufacturers face many operational challenges, and one of the most important is managing complex planning lines. However, AI integration presents a number of opportunities for optimization and improvement. Using IFS’s Planning and Scheduling Optimization module, manufacturing companies are already benefiting from AI-powered Visual Production Planning and Predictions. In addition, artificial intelligence extends to resource and location forecasting (Resource and Location Forecasting), a critical element in achieving production efficiency.
Using artificial intelligence, manufacturing companies can facilitate process optimization by employing advanced algorithms to examine data and identify areas for improvement, resulting in increased efficiency, reduced waste and energy savings.
AI as an Accelerator of Efficiency and Sustainability
AI represents more than just a technology tool; it is an accelerator that transforms manufacturing into a more efficient, sustainable and safer industry.
For example, the benefits of AI extend to autonomous vehicles and forklifts, which can control material handling and take shop floor operations to new levels. Artificial intelligence also simplifies the creation of asset maintenance checklists and provides valuable Asset Performance Management (APM) insights, enabling a shift from planned maintenance to truly predictive maintenance.
Quality Control and Waste Reduction
Minimizing industrial waste while ensuring quality is still a significant challenge; in fact, at least 50 percent of waste generated on a global scale comes from industrial production waste. To address this problem effectively, artificial intelligence has emerged as a promising solution to strike a delicate balance between quality control and waste reduction, improving our ability to make crucial, complex, high-volume decisions.
With AI-based systems, manufacturing companies can now optimize their operations and make more informed decisions, resulting in waste reduction and overall efficiency improvement. For example, a key application is found in Quality Control, where AI-driven computer vision systems take a leading role. These systems constantly examine products, ensuring a high-quality production standard while reducing the need for labor-intensive manual inspections.
Artificial intelligence extends to Product Lifecycle Management (PLM), influencing the entire product lifecycle, guiding design and manufacturing processes to achieve iterative improvements and superior quality results.
Process Monitoring and Anomaly Detection
Process Monitoring (PM) is another sphere that lends itself to the application of AI, offering real-time oversight of manufacturing processes. Through constant surveillance and timely adjustments, AI ensures quality integrity and continuous efficiency optimization. This dynamic, real-time control improves the entire production process.
In the field of anomaly detection, generative AI stands out as a “self-learning sentinel.” It continuously analyzes data streams, identifies normal patterns and refines its understanding of what constitutes an anomaly. This self-learning capability allows it to proactively detect and alert operators to emerging issues, enabling manufacturers to take corrective action before they impact production.
Implementing AI in your organization
First, by recognizing the indisputable importance of quality data, which is essential for making informed decisions, optimizing processes and ensuring product quality. Implementing measures to maintain data accuracy is therefore crucial. Next, a process assessment followed by the creation of a strategic plan is essential, with a focus on areas with the greatest potential for return on investment from AI integration. Finally, identifying bottlenecks and pain points in processes best suited for anomaly monitoring using AI.
Such monitoring provides valuable insights into the root causes of problems, facilitating their reduction. In summary, the journey begins with quality data, proceeds with strategic planning, and ends with active monitoring to continuously improve business efficiency.