Preventive and Predictive Maintenance: Examples and Differences
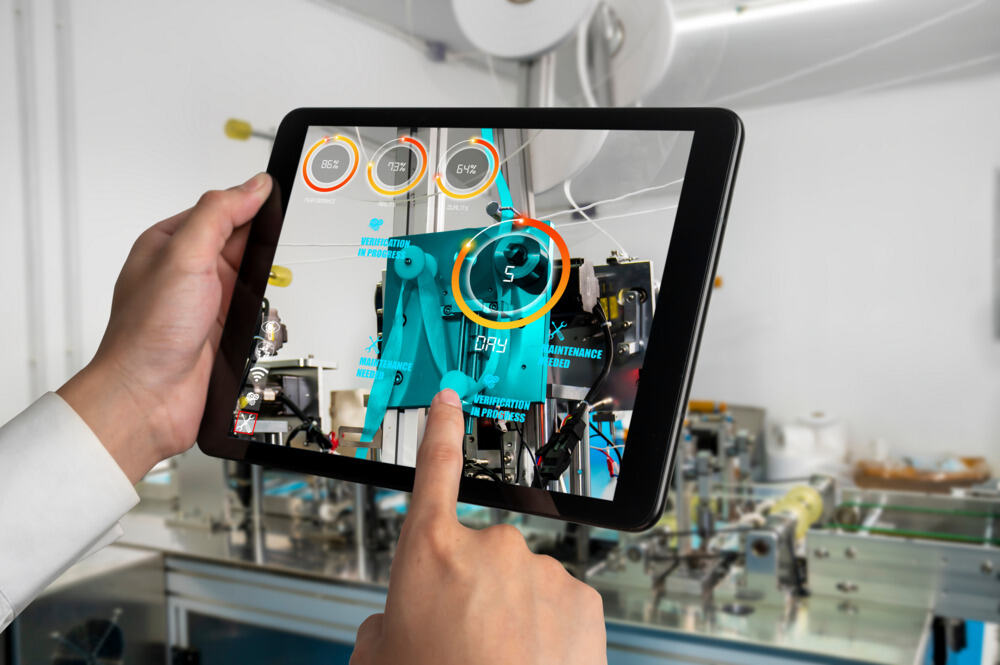
The key to ensuring productivity, safety, and competitiveness in the industrial context? Making sure that company assets operate at their maximum capacity, keeping machinery and equipment always in perfect efficiency. With the advancement of technology and increased performance expectations, companies must adopt increasingly sophisticated strategies to manage their assets.
Two distinct but complementary approaches stand out: preventive maintenance and predictive maintenance.
How Preventive Maintenance Works
Preventive maintenance is a traditional and systematic approach to asset management. The method relies on scheduled interventions at regular intervals, regardless of the actual condition of the asset. The main goal is to prevent breakdowns by replacing components and checking the operation of equipment. A typical example might be the periodic replacement of filters in an air conditioning system or the scheduled lubrication of industrial machines.
Another common example is the maintenance of production lines in factories, where machinery is inspected and calibrated according to a fixed schedule. The predefined planning aims to prevent critical equipment from failing during operations, thus ensuring continuous production and reducing downtime.
While this approach is effective in preventing sudden failures, it can be inefficient in terms of costs and resources as it does not consider the actual wear and tear of the assets. Often, still functional components are replaced, or maintenance interventions are carried out that may not be necessary. This can lead to waste and suboptimal use of company resources. Maintaining a strict maintenance schedule can also result in high costs, related both to the purchase of spare parts and the labor employed.
How Predictive Maintenance Works
Predictive maintenance stands out for its advanced use of modern technologies such as the Internet of Things (IoT), artificial intelligence (AI), and real-time data analysis. This approach relies on the continuous monitoring of the operational conditions of assets to predict and prevent failures before they occur. Advanced sensors collect data on various parameters, such as vibrations, temperature, and energy consumption, which are then analyzed to detect signs of deterioration.
IoT sensors installed on assets generate an enormous amount of data that is sent to cloud-based analytics platforms. Here, sophisticated machine learning algorithms analyze the data in real-time, identifying patterns and anomalies that may indicate performance degradation or an impending failure.
A practical example is the use of sensors to monitor the vibrations of an industrial motor. By analyzing the collected data, the system can identify anomalies that indicate an imminent need for maintenance, allowing for timely and targeted interventions. This way, it is possible to intervene only when necessary, based on concrete data rather than assumptions or predetermined intervals.
The benefits? Asset lifespan is extended; operational costs associated with unnecessary interventions are reduced, and unplanned downtime is minimized. All of this results in improved resource management.
Key Differences Between Preventive and Predictive Maintenance
Despite both approaches aiming to maintain asset efficiency and prevent failures, the differences between preventive and predictive maintenance are substantial. Let’s compare the two approaches.
Preventive Maintenance
- Fixed Scheduling: Preventive maintenance relies on fixed schedules, with interventions planned at regular intervals regardless of the actual condition of the assets.
- Proactive Approach: It prevents failures through regular interventions, such as component replacement and machine lubrication, to avoid sudden breakdowns.
- Standard Protocols: Uses standard protocols and maintenance manuals without the aid of advanced technologies.
- Cost and Resources: Can be inefficient in terms of costs and resources, as it does not consider the actual wear and tear of assets. Often involves replacing still-functional components.
Predictive Maintenance
- Real-Time Data: Predictive maintenance uses real-time data to plan interventions only when necessary, based on continuous monitoring of the operational conditions of assets.
- Advanced Technologies: Utilizes IoT sensors, cloud-based analytics platforms, and machine learning algorithms to collect and analyze large volumes of data.
- Flexibility and Responsiveness: This approach is more flexible and responsive compared to preventive maintenance, allowing for timely and targeted interventions only when they are actually needed.
- Initial Investments: Requires higher initial investments in technology and personnel training, but offers significant long-term savings by reducing operational costs and downtime.
- Resource Optimization: Enhances resource management and optimizes spare parts inventory, reducing warehouse costs and ensuring the availability of necessary parts at the right time.
Examples of Applications and Industry Uses
Both approaches find application in various sectors, often combined to maximize operational efficiency. In the manufacturing sector, preventive maintenance can be used to keep production lines running through regular checks and replacements. Predictive maintenance, on the other hand, allows real-time monitoring of critical machines, preventing failures that could interrupt production.
Similarly, in the energy and utilities sector, flexibility and innovation are necessary: IFS Cloud, for instance, enables users to balance priorities and incoming work, aiming to combine tasks and scheduled maintenance. These are just some of the reasons to choose the integration of IFS Cloud.
In the transportation sector, both techniques are also used to ensure the safety and reliability of vehicles, with preventive maintenance ensuring regular checks and predictive maintenance addressing detected anomalies.
IFS Solutions Offered by FI Solutions
For companies looking to effectively implement both approaches, the solutions offered by FI Solutions provide substantial support. Utilizing the advanced Enterprise Asset Management (EAM) systems by IFS, companies can integrate both preventive and predictive maintenance.
This allows them to tackle the challenges of the modern market and fully leverage the opportunities offered by digital transformation, improving performance and reducing operational costs.